In the fast-paced manufacturing world, asset availability, uptime, and reliability are more than just norms — they are critical factors that can make or break an entire business. Imagine a production line halting due to unexpected machinery breakdowns or a critical piece of equipment failing during a high delivery demand situation. The consequences can be devastating, leading to lost productivity, increased costs, financial implications, and dissatisfied customers.
In this blog post, we’ll delve into the strategies and best practices for maximizing uptime and reliability in industrial machinery. From understanding the importance of uptime to leveraging cutting-edge technologies, we’ll explore how businesses can minimize downtime and ensure continuous operations.
Understanding the Importance of Asset Uptime
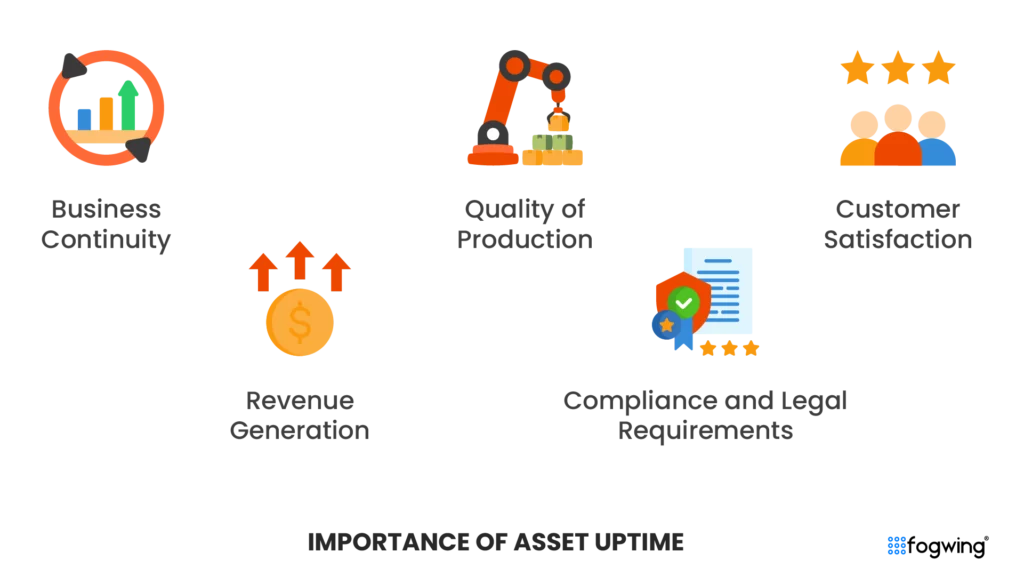
Asset uptime is when a system, particularly a machine or an entire ecosystem, is fully operational to produce goods or parts. Manufacturers invest heavily in the machinery to run the production operations. After heavy investment and continuous usage, the full yield takes time to meet ROI until machine availability through proper maintenance is crucial to accelerate the time to achieve ROI.
Understanding the importance of uptime is crucial, especially in the context of technology and business operations, for several reasons:
Business Continuity:
Asset uptime is essential for maintaining operations for many manufacturing businesses, especially those that rely heavily on machinery to run production operations. Any asset downtime can disrupt production, halt productivity, and result in financial losses. Since businesses heavily rely on asset productivity, the availability of fully functional assets is a lifeline for the manufacturers.
Quality of Production:
In manufacturing, production quality is critical, influencing customer satisfaction, brand reputation, and overall success. Reliable assets are pivotal in maintaining consistency, enhancing efficiency, and reducing costs. By investing in top-notch equipment, tools, and machinery, manufacturers uphold stringent quality standards, comply with regulations, and consistently meet customer expectations, fostering trust and loyalty while ensuring long-term competitiveness.
Customer Satisfaction:
Dependable assets play a pivotal role in meeting and surpassing customer expectations. Manufacturers achieve consistent quality, timely delivery, and product reliability through reliable equipment, machinery, and tools.
This reliability fosters customer trust and loyalty, driving repeat business and positive recommendations. Additionally, reliable assets enable swift adaptation to customer needs, optimizing production processes. Furthermore, these assets elevate customer satisfaction by minimizing defects and errors, enhancing the brand image.
Investing in reliable assets is not just a sound business strategy; it’s a cornerstone for sustained success in meeting customer demands and maintaining a competitive edge in the market.
Revenue Generation:
Unreliable assets in manufacturing operations can have significant financial ramifications, from escalated maintenance expenses to diminished revenue and profitability.
Frequent breakdowns or malfunctions incur repair costs and unplanned downtime, disrupting production schedules and causing delivery delays. This can lead to missed deadlines, contractual penalties, and customer dissatisfaction.
Furthermore, unreliable assets necessitate frequent replacements, increasing capital expenditures and reducing overall return on investment. Additionally, inefficiencies due to unreliable assets escalate labor costs, as employees may work overtime or resort to manual workarounds to mitigate equipment failures, further impacting the operation’s financial health.
Compliance and Legal Requirements:
Legal compliance is vital in manufacturing, but unreliable assets can hinder meeting regulations. Equipment failures pose safety and environmental risks, exposing the company to legal liabilities. Non-compliance tarnishes reputation and operational smoothness.
Only reliable assets may succeed in quality standards, leading to recalls and lawsuits. Maintaining reliable assets is crucial for regulatory adherence, workplace safety, and product quality assurance, safeguarding the company’s reputation and operations.
What is the reliability factor of an Industrial Machinery?
The reliability factor of a machine refers to its ability to consistently perform its intended function without failure or breakdown over a specific period under normal operating conditions. Reliability score is a key aspect of machine performance.
It is often quantified using metrics such as Mean Time Between Failures (MTBF), Mean Time To Repair (MTTR), Failure Rate, or Reliability Centered Maintenance (RCM) analysis.

Here are some key points regarding the reliability factor of a machine:
MTBF (Mean Time Between Failures):
MTBF measures the average time that elapses between consecutive failures of a machine or system. It is typically expressed in hours and is calculated by dividing the total operating time by the Number of failures experienced within that period. A higher MTBF value indicates greater reliability.
The formula to create the MTBF factor:
MTBF = Total uptime / Number of failures
MTTR (Mean Time to Repair):
MTTR measures the average time it takes to repair a failed system or component and restore it to operational status after a failure occurs.
The formula to calculate MTTR is:
MTTR = Total downtime / Number of failures
Failure Rate:
Failure rate refers to the frequency at which a machine or component fails within a given period. It is often expressed as the Number of failures per unit of time (e.g., failures per hour). Lower failure rates indicate higher reliability.
Predictive Maintenance:
Predictive maintenance techniques, such as condition monitoring and predictive analytics, can help assess the reliability of machines by identifying potential failure modes and scheduling maintenance activities before a breakdown occurs. This approach aims to maximize uptime and minimize unexpected downtime.
Reliability Engineering:
Reliability engineering involves designing, testing, and optimizing machines and systems to achieve desired levels of reliability. It often involves techniques such as Failure Mode and Effects Analysis (FMEA), reliability testing, and design for reliability.
Factors Affecting Reliability:
The reliability of a machine can be influenced by various factors, including design quality, component selection, manufacturing processes, operating conditions, maintenance practices, and environmental factors. Identifying and mitigating potential sources of failure can improve overall reliability.
Continuous Improvement:
Reliability is not a static attribute but rather a dynamic characteristic that can be continuously improved over time through feedback, analysis of failures, and implementation of corrective actions. Continuous improvement efforts are essential for maintaining and enhancing machine reliability.
How to create a strategy for maximizing Asset Uptime?
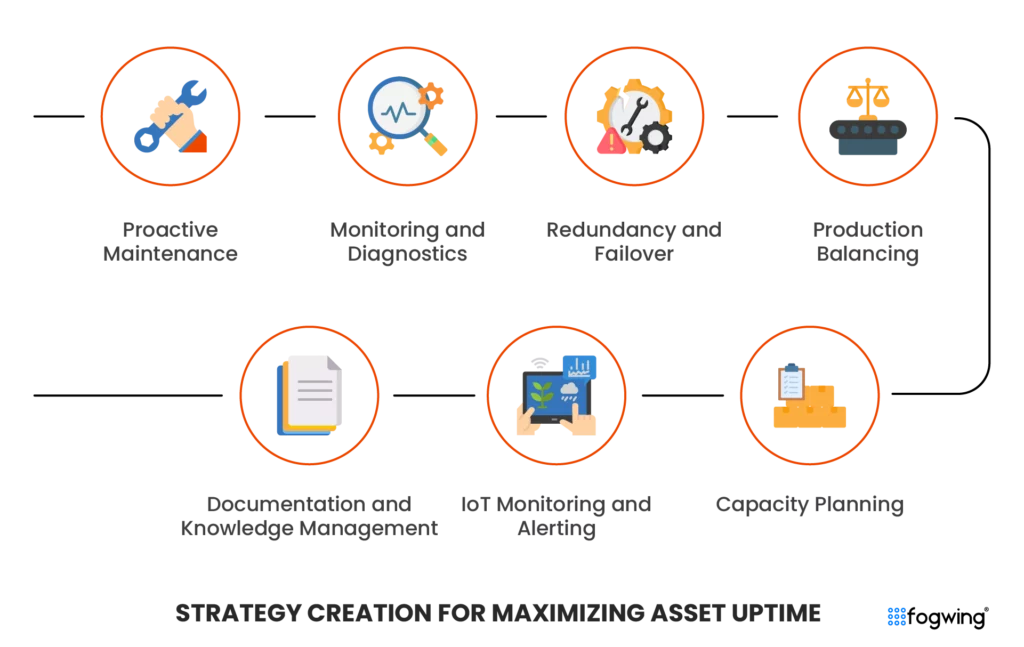
Maximizing asset uptime is essential for ensuring the smooth operation of systems, minimizing disruptions, and maintaining productivity. Here are some strategies for maximizing uptime:
Proactive Maintenance:
Implement proactive maintenance practices such as preventive, predictive, and reliability-centered maintenance to increase the asset availability for production. Regularly scheduled inspections, lubrication, calibration, and replacement of worn parts can help prevent unexpected breakdowns and prolong equipment lifespan.
Monitoring and Diagnostics:
Utilize IoT monitoring systems and diagnostic machines to continuously track the health and performance of critical equipment parameters. Real-time data analytics, IoT sensor technology, and asset condition monitoring can help identify potential issues early and take proactive measures to address them before they escalate into failures.
Redundancy and Failover:
Implement redundancy and failover mechanisms for critical systems and components. This may include redundant power supplies, backup generators, mirrored production centers, parts backup, and failover clustering for high availability.
Production Balancing:
Distribute production across multiple assets or machines to prevent overloading and optimize asset utilization. Production balancing techniques can help distribute demands or process work orders evenly, reducing the risk of machine failure earlier than predicted.
Capacity Planning:
Conduct regular capacity planning assessments to ensure systems have adequate resources to handle current and future demands. Anticipating growth trends and scaling resources pre-emptively can help avoid performance bottlenecks and downtime caused by resource constraints.
IoT Monitoring and Alerting:
Implement IoT monitoring and alerting systems to detect real-time anomalies, performance degradation, and potential failures. Automated alerts can notify the maintenance team promptly, allowing them to take corrective actions before issues escalate.
Documentation and Knowledge Management:
Maintain comprehensive documentation of systems, configurations, maintenance procedures, and troubleshooting guidelines. Centralized knowledge management systems can streamline troubleshooting efforts and facilitate rapid resolution of issues, reducing downtime.
How does Fogwing Asset+ help in reliability management?
Fogwing Asset+ CMMS Software offers an Asset 360 module, which provides a 360-degree view of asset information in a single module. Fogwing helps to capture the asset downtime, duration, and fault reasons as part of the work order execution and IoT metering. This data set helps to identify and calculate the asset reliability factors such as MTTR, MTBF, Asset Health Score, Reliability score, and failure rate.

Asset 360 view provides these data in a single dashboard for high visibility and actionable insights. Customers using Fogwing Asset+ software gain access to this feature, which enables them to reduce downtime by up to 40% and increase overall machine productivity by up to 35%.
Conclusion:
Final wordings, maximizing uptime and reliability is not just a goal—it’s a necessity. Businesses can minimize downtime and ensure continuous operations by understanding the importance of uptime, implementing proactive maintenance strategies, leveraging technology, and adopting best practices. By prioritizing uptime and reliability, businesses can drive productivity, optimize efficiency, and thrive in today’s competitive marketplace.
