In today’s fast-paced industrial landscape, maintenance professionals are often bogged down by traditional maintenance management practices like reactive maintenance, manual entry, miscommunication, and unexpected downtime.
Industry maintenance management inefficiencies drain resources and compromise asset performance and business. According to a Deloitte report, unplanned downtime costs manufacturers over $50 billion annually.
Enter CMMS work order management powered by AI. These help the maintenance team automate work order creation, prioritize resource allocation, and provide real-time data optimizations, boosting productivity and reducing workload.
This blog explores the agile, proactive, cost-effective CMMS work order system that helps organizations shift from reactive to proactive maintenance.
What is an AI-powered CMMS?
A Computerized Maintenance Management System (CMMS) centralizes, automates, and streamlines asset maintenance activities such as maintenance work order creation, inventory tracking, asset management, and work order tracking.
An AI-powered CMMS goes further by incorporating artificial intelligence to enhance maintenance operations. It helps the maintenance team to analyze data, automate decisions, and improve maintenance strategies in work order software.
How AI Transforms CMMS:
- Real-time data analysis: It analyses the real-time asset data and historical data captured by sensors in real-time to make a fast, informed maintenance decision.
- Predictive maintenance capabilities: An AI-powered CMMS work order management utilizes AI and Machine learning tools to forecast asset failures before they occur.
- Intelligent Task Prioritization and allocation: Automatically assigns and schedules work orders based on urgency, technician availability, and asset criticality.
Traditional vs. AI-Powered CMMS: A Quick Comparison
Feature | Traditional CMMS | AI-Powered CMMS |
Scheduling | Maintenance is scheduled on fixed dates or runtime thresholds, often missing early signs of failure. | Uses real-time asset health data and predictive models to schedule asset maintenance only when needed, minimizing unnecessary tasks and downtime. |
Work Order Assignment | Supervisors assign Tasks manually, which may result in inefficiencies or misallocation of skills. | AI automatically evaluates technician skill sets, task urgency, availability, and historical performance to assign the right job to the right person. |
Downtime Handling | Teams react only after equipment fails, leading to unplanned downtime and costly repairs. | AI monitors asset behaviour continuously, predicting potential failures in advance and triggering proactive maintenance actions. |
Resource Management | Inventory and workforce planning are handled separately, often leading to delays or part shortages. | Integrates real-time inventory data, technician schedules, and task priorities to optimize resource availability and usage. |
Communication | Relies on slow and fragmented methods like emails, paper forms, or walkie-talkies. | Sends instant alerts, mobile notifications, and status updates to all stakeholders through the CMMS word order system or mobile app. |
Data Usage | Uses static, after-the-fact reports that provide limited decision-making support. | Continuously analyzes live and historical data to provide actionable insights, KPIs, and trend forecasts. |
Documentation | Work orders, compliance logs, and maintenance history are recorded manually, increasing the risk of errors. | It auto-generates, updates, and stores digital records in real time, ensuring accuracy and audit readiness in the work order software. |
Scalability | Growth requires more manual input, staff, and complex coordination, which becomes unsustainable. | AI automates repetitive tasks and scales effortlessly, making it suitable for growing operations without increasing overhead. |
How AI Enhances Work Order Management
Here’s a benefit-driven explanation of how AI enhances work order management.
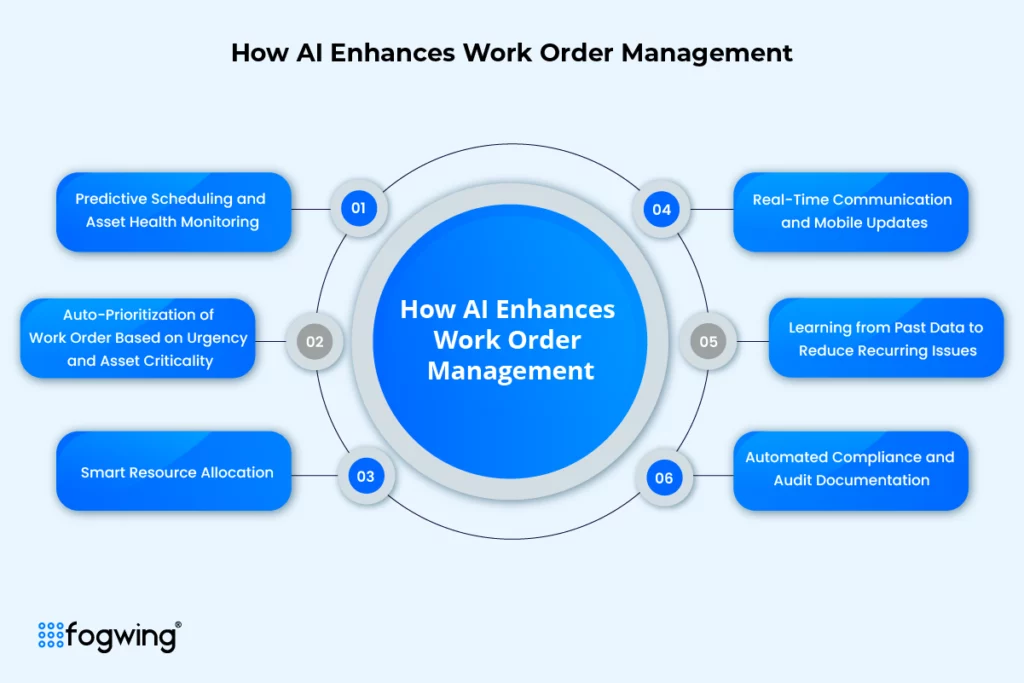
- Predictive Scheduling and Asset Health Monitoring:
Traditional maintenance systems constantly rely on calendar-based preventive and reactive maintenance, eventually leading to unnecessary downtime or missed asset failures.
An AI-powered CMMS Work Order Management utilizes real-time data from IoT sensors and historical performance data to continuously evaluate the asset condition.
It enables the maintenance team to schedule asset maintenance only when required, reducing asset downtime, extending asset life, and efficiently utilizing labour and resources.
- Auto-Prioritization of Work Order Based on Urgency and Asset Criticality:
AI enhances the work order management software by ranking the maintenance tasks based on due date and asset criticality. It analyses how severe the issue is and how critical the asset is for the organization.
For example, a slightly high temperature in the production motor might trigger a high-priority maintenance work order, while a minor lighting fault in the inventory would be deprioritized.
With its advanced intelligent technologies, AI-powered CMMS Work Order Management ensures that the maintenance team focuses on what matters and prevents production bottlenecks.
- Smart Resource Allocation:
Manually assigning the right technicians with the right tools and parts to the right job is always error-prone. So, it’s where work order management software helps organizations.
A CMMS software evaluates the maintenance technicians’ certification, skill sets, and availability and allocates the required tools and parts. It keeps track of inventory levels and ensures the tools and spare parts are available before assigning a job.
A CMMS work order system eventually helps organizations reduce job delays, maintenance costs, and inefficiency.
- Real-Time Communication and Mobile Updates:
A CMMS software seamlessly integrates with mobile devices and provides real-time, simplified communication across the maintenance team.
The Maintenance technicians will receive notifications, alerts, instructions, and updates on their mobile apps, eliminating the need for follow-up emails, paper trails, and manual follow-ups.
A CMMS Work Order Management mobile application helps maintenance managers and supervisors track progress, assign maintenance work orders, manage inventory, and close work orders digitally.
The connected ecosystem and the real-time data provided by the work order management software ensure transparency, accountability, and faster task resolution.
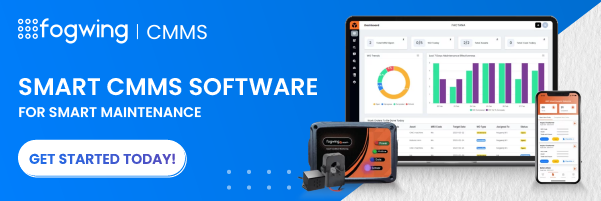
- Learning from Past Data to Reduce Recurring Issues:
AI systems analyze historical maintenance logs to detect patterns and root causes behind frequent breakdowns.
For example, if a specific pump fails every 60 days due to a worn seal, the CMMS work order system can flag it for early intervention or recommend an alternative part.
This form of continuous improvement reduces repetitive work orders, prevents recurring failures, and enables maintenance teams to shift from reactive to truly proactive strategies.
- Automated Compliance and Audit Documentation:
Regulatory compliance often requires detailed documentation of maintenance actions, timelines, personnel involved, and asset performance.
AI-powered CMMS work order management auto-logs every action—from work order creation to task completion—with digital signatures and timestamped data.
It generates real-time audit-ready reports, simplifies inspections, and reduces the administrative burden on maintenance teams. This not only ensures compliance but also enhances transparency and traceability.
Challenges of AI-Powered CMMS
- High Initial Investment: Implementing AI-enabled CMMS software often requires significant upfront software, hardware, and integration costs.
- Data Quality and Availability: AI models rely heavily on accurate, historical maintenance data. Inconsistent or incomplete records can reduce the effectiveness of predictive maintenance.
- Integration Complexity: Merging AI-powered CMMS work order management with existing ERP, IoT, or legacy systems can be technically challenging and time-consuming.
- User Adoption and Training: Maintenance teams may struggle to adopt AI features without proper training, especially if they’re used to manual or traditional systems.
- Cybersecurity Risks: AI-integrated systems that connect to cloud networks and IoT devices increase exposure to cyber threats, requiring robust security protocols.
- Overreliance on Automation: Excessive dependence on AI recommendations may lead to reduced human oversight and missed critical anomalies.
- Regulatory Compliance: AI algorithms must be transparent and auditable to meet industry regulations, especially in sectors like oil & gas and pharmaceuticals.
- Scalability Challenges: Not all AI solutions scale effectively across multiple sites or geographies with different asset types and workflows.
How to Overcome the Adoption Challenges of AI-Powered CMMS
Implementing an AI-powered CMMS work order management system brings significant productivity benefits, but successful adoption depends on managing the organizational change effectively. Here’s how to overcome common barriers:
1. Provide Role-Based Training
- Develop training programs tailored to different user roles—technicians, supervisors, and IT teams.
- Focus on how AI tools augment existing workflows rather than replace human roles.
- Demonstrate the practical benefits of AI features like predictive scheduling and auto-prioritization.
2. Prioritize a User-Friendly Interface
- Choose CMMS platforms with an intuitive and accessible UI/UX.
- Ensure a minimal learning curve to reduce resistance to new technology.
- Highlight how users can easily navigate and interact with AI-driven work order software features.
3. Implement Phased Adoption
- Start with high-impact assets or departments to prove quick value.
- Gradually scale usage across teams and sites to allow a smooth transition.
- Use early wins to build internal momentum and trust in the system.
4. Address Cultural and Psychological Barriers
- Acknowledge and address fears of job displacement and AI uncertainty.
- Educate teams on how AI supports and enhances human decision-making.
- Reinforce data trust by explaining how AI responsibly uses historical and real-time data.
5. Communicate Vision and Long-Term Gains
- Leadership should clearly articulate the strategic goals of adopting AI-powered CMMS work order management.
- Emphasize long-term productivity improvements, cost savings, and job empowerment.
- Create a feedback loop to involve users in system improvement and keep them engaged.
Metrics to Track Productivity Gains
Organizations must focus on clear, data-driven KPIs to measure the real impact of an AI-powered CMMS work order system. These metrics help quantify improvements in productivity, efficiency, and asset reliability.
- MTTR (Mean Time to Repair): AI streamlines diagnostics and automates work order assignment, significantly reducing the average time required to repair equipment. A drop in MTTR directly indicates improved response and resolution speeds.
- Planned vs. Unplanned Maintenance: A high ratio of planned to unplanned tasks signals proactive, predictive maintenance. AI-driven work order management scheduling helps shift maintenance from reactive to preventive, reducing costly breakdowns.
- Asset Uptime & Technician Productivity: With predictive alerts and optimized task allocation, technicians spend less time troubleshooting and more time performing value-added tasks. Increased asset uptime reflects fewer disruptions and longer operational periods.
- Work Order Completion Rate: An upward trend in CMMS work order management shows how automation is helping teams close more tasks on time, leading to better resource utilization and faster turnaround.
Tracking these KPIs allows businesses to validate the ROI of their AI-powered CMMS and continuously refine their maintenance strategies.
The Future of Work Order Management with AI
Advanced AI technologies beyond automation are shaping the next frontier in work order management.
AI-powered CMMS platforms rapidly evolve into intelligent systems that integrate seamlessly with other cutting-edge tools.
- Digital Twins: By creating real-time virtual replicas of physical assets, digital twins allow AI to simulate performance, detect anomalies, and predict maintenance needs before failure occurs.
Maintenance work orders are generated automatically based on these insights, enhancing precision and reducing guesswork.
- Generative AI for Reporting: Reporting no longer must be manual or time-consuming. Generative AI in CMMS work order management can analyze thousands of data points and instantly produce natural-language summaries, dashboards, and actionable insights for maintenance managers. It makes decision-making faster and more data-driven.
- AR for Troubleshooting: Augmented Reality (AR) revolutionizes technician support. With AI-guided AR overlays, technicians can visualize repair instructions, part locations, and real-time diagnostics. This reduces errors, improves safety, and accelerates task completion.
Conclusion
Fogwing CMMS, powered by AI, transforms traditional maintenance into a proactive, intelligent process. Automating work order creation, predicting asset failures, and optimizing technician assignments helps organizations reduce downtime, boost productivity, and improve asset reliability.
Despite adotion challenges, Fogwing’s user-friendly interface, mobile accessibility, and phased implementation support make the transition smoother.
The value of work order software becomes clear when paired with measurable KPIs like MTTR and work order completion rates.
As CMMS work order management software evolves with innovations like Digital Twins, Generative AI, and AR support, it empowers maintenance teams to stay ahead and build more intelligent, data-driven operations for the future.
FAQs
1. What features should I look for in an AI-based work order management system?
When choosing an AI-powered work order management system, look for the following key features:
- Predictive Maintenance
- Automated Work Order Creation & Scheduling
- Real-Time Asset Condition Monitoring
- Skill-Based Technician Assignment
- Mobile Access
- IoT Integration
- Intelligent Dashboards
2. What industries benefit most from AI in work order management?
Industries that rely heavily on asset reliability and uptime derive the most value. These encompass manufacturing, utilities, oil and gas, transportation, facilities management, and food processing. AI assists these sectors in reducing downtime, managing compliance, and optimizing maintenance operations.
3. What is AI-powered work order management?
AI-powered work order management leverages AI to automate creation, prioritization, scheduling, and completion of maintenance tasks. It uses real-time data, historical trends, and asset criticality to ensure more innovative, faster, and proactive maintenance workflows.
4. How does AI improve work order management efficiency?
AI boosts efficiency by reducing manual input, automating decisions, predicting asset failures, optimizing technician assignments, and streamlining communication. Platforms like Fogwing CMMS help teams resolve issues faster, reduce maintenance costs, and improve asset uptime.
5. Is AI-powered cmms work order management expensive to implement?
AI-powered systems are more affordable than ever. Cloud-based platforms like Fogwing CMMS offer flexible, subscription-based pricing with minimal infrastructure costs. Over time, the productivity gains and cost savings often outweigh the initial investment.
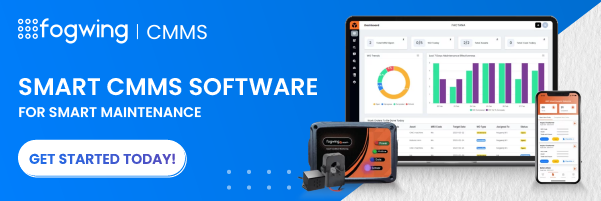