Manufacturing industries rely heavily on automation machinery and equipment for daily productivity. Any machine downtime during production will have a financial impact due to non-productive work hours, quality degradation, and delivery delays.
The traditional approach to asset maintenance through papers, whiteboards, and job cards failed due to a lack of traceability and accountability.
A CMMS (Computerized Maintenance Management System) streamlines maintenance workflows, reduces unexpected breakdowns, and enhances productivity.
This best practice guide analyzes the practices and key insights for leveraging CMMS for manufacturing at its fullest potential.
What is CMMS for Manufacturing?
CMMS for manufacturing refers to specialized maintenance management software designed to manage and optimize maintenance operations within manufacturing plants.
Unlike generic CMMS solutions, manufacturing-focused systems address the unique demands of high-volume production, complex machinery hierarchy, IoT data, prevention, prediction, regulatory compliance, and strict safety protocols.
CMMS for manufacturing provides features and functions to centralize assets master, parts inventory, and maintenance tasks, from preventive maintenance scheduling to real-time asset monitoring, providing unparalleled visibility and traceability to managers and maintenance teams.
Why CMMS is Essential for Manufacturing
Since production operations rely heavily on machinery’s continuous function to meet delivery schedules and revenue targets, a single equipment failure in the production process can cascade into production halts, missed deadlines, and financial losses.
CMMS for manufacturing offers multiple benefits that directly improve the operational processes:
- Minimize unplanned downtime through proactive maintenance.
- Prolong equipment lifespan with consistent, data-driven care.
- Simplify regulatory compliance with automated record-keeping.
- Enhance workplace safety by ensuring proper inspections and maintenance routines.
- Provide actionable insights with real-time performance data.
Best Practices for Implementing CMMS for Manufacturing
Even though CMMS for Manufacturing offers many features and functions specific to the manufacturing business, adaptability and usability require some best practices for high results.
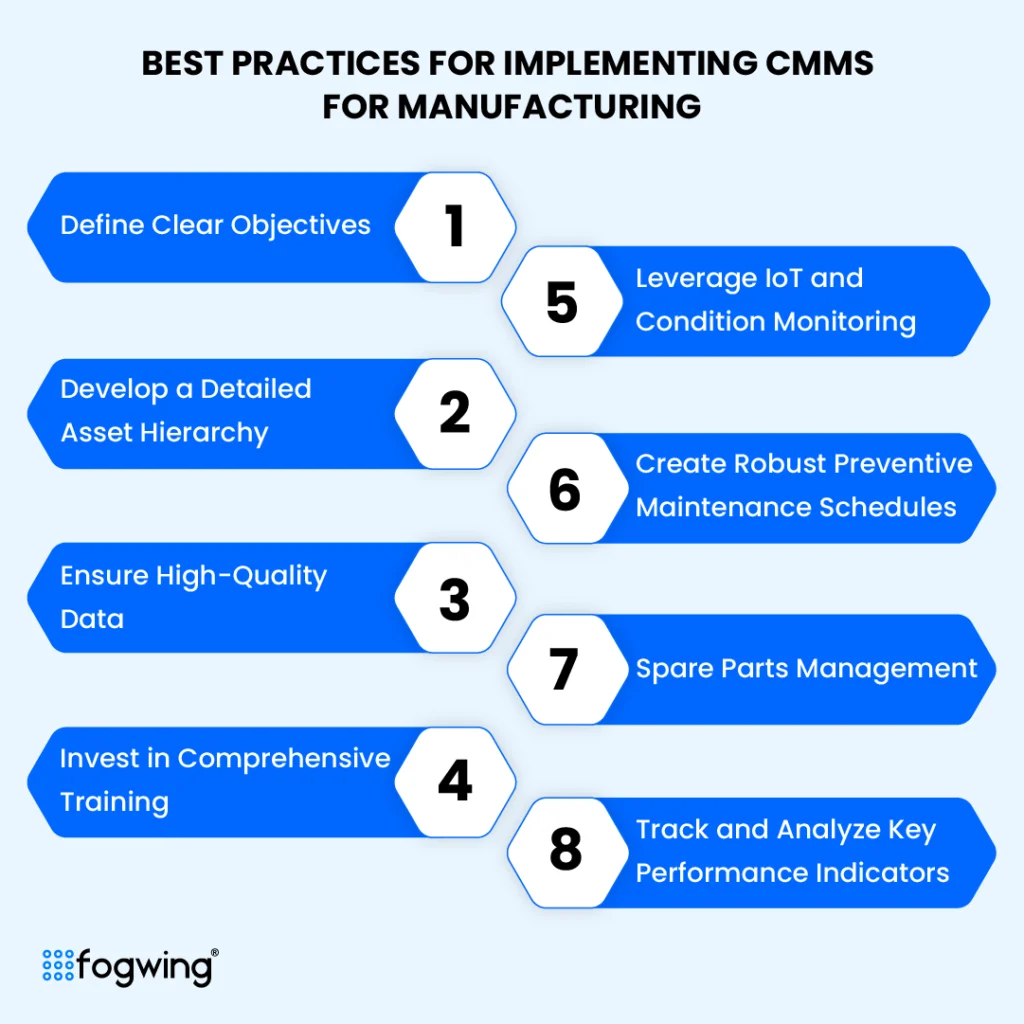
1. Define Clear Objectives:
If you want to establish a very effective maintenance strategy that requires discipline in day-to-day activities. In order to bring discipline in work activities, It is important to establish a system operating procedure (SOP) based on the asset hierarchy and history of data, set measurable goals (SLAs), and track work completion against it before implementing CMMS for manufacturing.
Whether aiming to reduce downtime by 25% or improve inventory accuracy, clear objectives ensure the system delivers targeted results.
2. Develop a Detailed Asset Hierarchy:
The maintenance and plant operations teams must logically understand assets’ structure by categorizing sub-equipment, usage lifecycle, criticality, function, and location to stream maintenance activities.
Asset hierarchy helps to improve work order planning, work execution, and enforcing operating procedures for reporting across organizations.
3. Ensure High-Quality Data:
The most important best practice is managing the clean data for accurate maintenance operations. So, establishing accurate Asset master and transactional data is the foundation of an effective CMMS implementation.
A periodic data audit of asset master, maintenance histories, and inventory records helps to ensure a reliable system for the maintenance team to follow trusted operations.
4. Invest in Comprehensive Training:
The most challenging part of CMMS is user adoption. A very successful CMMS implementation depends on user acceptance and ease of usage.
Training and skill development are critical practices for technicians, supervisors, and managers to leverage CMMS software at its full scale to simplify their daily tasks, and improve performance.
5. Leverage IoT and Condition Monitoring:
The advanced CMMS software for the manufacturing industry supports IoT integration natively.
Industrial Internet of Things (IIOT) allows engineers to connect IoT devices to the assets to measure the asset usage and critical sensor parameters for real-time condition monitoring.
The aggregated machine sensor (ex: vibration, temperature, and pressure) data helps predict failures, enabling predictive maintenance.
6. Create Robust Preventive Maintenance Schedules:
Traditionally, the maintenance team is familiar with preventive maintenance. Instead, we leverage manufacturer guidelines, operational data from IoT and systems, and expert input to develop effective preventive maintenance schedules. CMMS for manufacturing software (ex, Fogwing) provides a PM (preventive maintenance) traceability module to track the PM effectiveness.
7. Spare Parts Management:
The modern CMMS software provides parts inventory management as part of the CMMS, letting us leverage CMMS features to monitor spare parts usage, automate reorder points, and maintain an optimal inventory balance, avoiding stockouts and excess inventory.
The mobile-friendly CMMS allows field technicians to check the part’s availability, reservations, and traceability features from anywhere and at any time.
8. Track and Analyze Key Performance Indicators (KPIs):
CMMS’s analytical and reporting capabilities for manufacturing are used to monitor KPIs like MTBF(Mean Time Between Failure), MTTR(Mean Time To Repair), and schedule compliance, identifying areas for continuous improvement.
Common Challenges in Adopting CMMS for Manufacturing:
While CMMS software provides various process and operational capabilities, it is also important to understand the challenges in adoption.
Resistance to Change:
The biggest challenge in CMMS implementation for manufacturing is adaptability by the maintenance team. Many CMMS implementations failed since the frontend team did not practice the tools provided to the fullest possibilities.
We must engage maintenance teams early in the implementation process to overcome this challenge. The implementation and governance team should demonstrate how CMMS for manufacturing improves efficiency and job satisfaction.
Data Migration:
Every manufacturer has been practicing maintenance operations for decades using papers, excel sheets, or legacy ERP, and moving them to digital CMMS requires careful data porting from existing legacy maintenance systems to newer CMMS.
The best practice is to begin with essential master data fields such as assets and parts inventory first and gradually adopt advanced features as users become more familiar with the system.
Integration Complexities:
It is important to continue the collaborative operational practices by integrating CMMS with existing enterprise applications such as ERP/MRP, MES, Inventory, and financial systems.
Most of the modern CMMS for manufacturing offers open API integration support to ensure seamless connectivity with ERP, MES, and SCADA systems.
The Future of CMMS for Manufacturing
CMMS is becoming critical in transforming maintenance operations as a central hub for operational teams for predictive maintenance, operational optimization, and decision-making.
The digital leaders in the manufacturing industry are adopting AI-powered CMMS software to increase asset reliability, reduce operational costs, and enhance competitive advantage.
Advanced CMMS for manufacturing extends beyond basic maintenance management, offering strategic benefits that drive long-term operational excellence:
- Root Cause Analysis: RCA helps to analyze the root of the failure to identify the machine problems, process inefficiencies, and operator errors. Once the source of the problem is identified, a corrective action will be recommended to prevent the failure again.
- AI-Driven Predictive Maintenance: AI-powered CMMS software helps to analyze the data to identify anomaly conditions, then, based on history, find the next failure possibilities, predicting maintenance requirements.
- Mobile-Enabled Maintenance: Empower technicians with mobile access to work orders, equipment history, and real-time updates, improving field efficiency and data accuracy.
- Sustainability and Energy Efficiency: Monitor and optimize energy consumption, reducing environmental impact and supporting corporate sustainability initiatives.
- Regulatory Compliance Automation: CMMS also helps to generate work compliance summary reports which can be used as process compliance documents for safety certifications, inspection records, and simplifying compliance with ISO, OSHA.
Best CMMS Software for Manufacturing
Choosing the right CMMS for manufacturing is critical to achieve a high return on investment from the digital practice.
Here are some of the top CMMS software solutions specifically designed for manufacturing environments:
Fogwing CMMS
Fogwing CMMS stands out as a comprehensive and intelligent CMMS solution for manufacturing industries. Fogwing CMMS combines traditional maintenance management practices with modern IoT integration, AI-powered capabilities to achieve real-time asset monitoring, RCA, and intuitive mobile access.
With Fogwing CMMS, manufacturers gain full visibility into their asset health, streamline maintenance operations, ensure regulatory compliance, and achieve superior operational efficiency.
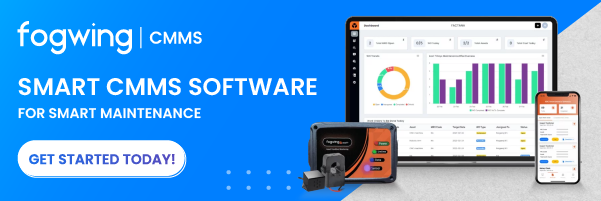
Fiix CMMS
Fiix offers user-friendly maintenance management with cloud-based flexibility. It provides preventive maintenance scheduling, work order management, and reporting features that cater well to mid-sized manufacturing operations.
UpKeep CMMS
UpKeep is known for its mobile-first approach, making it easy for technicians to access work orders and asset data. It’s ideal for teams looking for a simple, accessible solution with strong mobile functionality.
MaintainX
MaintainX offers real-time collaboration, simple work order management, and compliance tracking. Its intuitive design makes it popular for small to medium manufacturing facilities.
Hippo CMMS
Hippo CMMS balances functionality and simplicity, offering preventive maintenance, asset management, and reporting features that serve diverse manufacturing needs.
When you are evaluating CMMS for your manufacturing, you must consider factors such as manufacturing-specific process support, asset management, production data capturing, alignment with product scheduling, integration capabilities, and user adoption.
Fogwing CMMS, with its smart feature set and industry-ready architecture, is particularly well-suited for manufacturers seeking to embrace Industry 4.0 and achieve long-term maintenance excellence.
Conclusion:
CMMS software is not an option for asset maintenance and operational teams; it is a necessary tool for manufacturers to automate maintenance operations for seamless operations. Asset-intensive industries can transform maintenance operations by following best practices.
When you select the best CMMS for your manufacturing operations, you can achieve higher asset uptime, environmental safety, and more efficient production lines, ultimately driving long-term business success.
FAQs
1. What is CMMS software used for in manufacturing?
CMMS (Computerized Maintenance Management System) software is used in manufacturing to keep machines running smoothly. It helps track maintenance schedules, work orders, and equipment history, so teams can fix issues before they become problems and avoid costly production delays.
2. How does CMMS reduce costs?
A good CMMS helps you stay ahead of breakdowns by keeping maintenance on schedule. That means fewer surprises, less emergency overtime, and no scrambling for parts. Over time, it lowers repair bills, keeps your equipment in better shape, and cuts unnecessary downtime—all of which add up to real savings.
3. Can small manufacturers use CMMS?
Yes, Many CMMS platforms are affordable, cloud-based, and easy to use—perfect for small and mid-sized manufacturing businesses.
4. What industries benefit the most from CMMS?
CMMS software is valuable across industries, but it’s especially beneficial in:
- Manufacturing
- Food and Beverage
- Automotive
- Pharmaceuticals
- Energy and Utilities
5. What are the top 5 CMMS software solutions for manufacturing?
- Fogwing CMMS
- Fiix CMMS
- UpKeep CMMS
- MaintainX
- Hippo CMMS
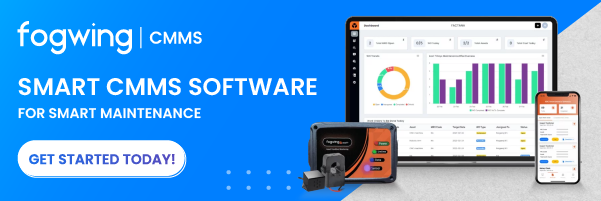